|
|
Noticias
|
|
Todo sobre aceros inoxidables |
En este artículo te vamos a contar todo sobre el acero inoxidable, un aliado estratégico en la composición de nuestros productos. Conocé sus ventajas, sus principales características y las principales aplicaciones de una aleación que garantiza el éxito en los procesos industriales.
La resistencia a la corrosión de los aceros inoxidables se debe a una delgada película de óxido de cromo que se forma en la superficie del metal como consecuencia de los agregados de distintos elementos, como níquel, cromo, molibdeno, titanio y otros que confieren cada uno distintas propiedades. A pesar de ser sumamente delgadas, estas películas invisibles, fuertemente se adhieren al metal, lo protegen contra los distintos tipos de corrosión, renovándose inmediatamente cuando es dañada por abrasión, corte, etc. Sin embargo en determinadas ocasiones también el acero inoxidable puede ser atacado por el fenómeno más común que es la corrosión.
Según el uso, habrá que utilizar las aleaciones más aptas para defenderse. La más común es la corrosión galvánica que describimos a continuación:
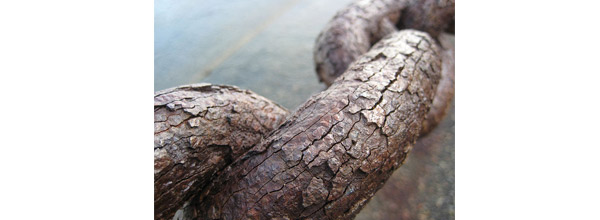
Corrosión galvánica
Sobreviene cuando entre dos metales distintos se forma una unión que está sumergida en una solución que puede obrar como electrolito. Se realiza en un medio corrosivo por dos electrodos cortocircuitados , constituyéndose una celda electroquímica. De ello resulta la disolución del electrodo anódico, mientras que el catódico permanece inalterable.
Tipos de aceros inoxidables
Las estructuras de las distintas aleaciones con que se cuenta en la actualidad pueden agruparse en tres distintos tipos de acero inoxidable:
• Austeníticos • Martensíticos • Ferríticos
La sigla AISI significa “American, Iron and Steel Institute”.
Aceros inoxidables austeníticos: Se caracterizan por tener muy buena resistencia a la acción de los agentes atmosféricos y por los aceros que tienen la mayor resistencia a la acción corrosiva de los ácidos, resistir altas temperaturas y buena resistencia mecánica y a la oxidación.
• AISI 301: Tiene menos cromo y níquel que cualquiera de la serie austenítica, siendo su empleo restringido para los casos de ataques corrosivos moderados. • AISI 302: Resulta más resistente a la corrosión, es muy dúctil y apto para estampados profundos. • AISI 304: Acero de bajo contenido de carbono con mejor resistencia a la corrosión en estructuras soldadas. • AISI 316: Acero que incorpora molibdeno en su composición química, mejorando notablemente sus características anticorrosivas a distintos agentes químicos. • AISI 316L: Es un acero especial, recomendado en los casos que la precipitación de carburo en las uniones soldadas sea indeseada.
Aceros martensíticos: En los aceros inoxidables martensíticos se concentra un alto porcentaje de carbono y son magnéticos además de contener cromo en cantidades entre el 11,5 y 18% y carbono entre el 0,1 y el 1,5%.
• AISI 403 y 410: Son aceros inoxidables necesariamente muy resistentes y pueden templarse, tienen buena resistencia a la corrosión. Se utilizan en la fabricación de álabes de turbinas, elementos rotantes de bombas, bulonería, columnas de destilación, y en la industria petroquímica. • AISI 420: Son aceros de alto contenido de carbono, muy resistentes y aptos para transmitir potencia. Mediante tratamiento térmico se lo utiliza en la fabricación de herramientas. Tiene la propiedad de ser magnético.
Aceros ferríticos: Son aceros de alto contenido de cromo, entre el 15 y 27% y muy poco carbono. Son magnéticos, resistentes a la corrosión pero no muy resistentes a impactos.
• AISI 430: Es dúctil y se lo utiliza para plantas industriales con presencia de ácido nítrico, uno de los más agresivos.
Foto corrosión: By Marlith - Creative Commons Attribution-Share Alike 3.0 Unported |
|
|
|
|
|